生産効率向上、新素材への対応、コスト削減など、製造現場の課題を解決に導く「次世代の切り札」として、製造現場で注目を集めているレーザー加工機。
しかし「そもそもレーザー加工機とは何か」「具体的にどんな加工ができるのか」「従来の加工方法と比べてどんな強みがあるのか」といった疑問をお持ちの方も多いのではないでしょうか。
レーザー加工機の導入を検討する際は、機種ごとの導入コストや運用負担を考慮することが重要です。特に溶接機は比較的手頃な価格で導入可能な一方、切断加工機は初期投資が高額となるため、外注の活用も有効な選択肢となります。
本記事では、レーザー加工機の基礎知識から最新技術動向、導入メリット、機種選定のポイント、導入・運用時の注意点まで、実務に役立つ情報を網羅しました。レーザー加工機の導入を検討する際の判断材料としてご活用ください。
レーザー加工機とは
レーザー加工機は、レーザー光を熱源として材料の切断、溶接、マーキングなどを行う工作機械ですが、機能や用途により大きく分けられます。
特に、溶接機は数百万円程度で導入可能な場合が多く、部品接合に適した装置です。一方、切断加工機は、数千万円から1億円を超えるコストがかかり、高精度な切断や大型材料の加工に対応します。
レーザー加工機の基本的な仕組み
レーザー加工機は、高出力で集中したレーザー光を用いて材料を加工する工作機械です。通常の光と異なり、レーザー光は極めて高いエネルギーを持ち、非常に細く絞られた光線として照射されます。
このため、金属から樹脂まで幅広い素材に対して、高精度な加工を実現することができます。
レーザー光の発生原理
レーザー光は、「誘導放出による光増幅」という物理現象を基に生成されます。まず、外部から物質にエネルギーを与えることで、電子が低エネルギー状態から高エネルギー状態(この過程を「励起」と呼ぶ)になります。高エネルギー状態の電子は不安定であり、元の低エネルギー状態に戻る際に光を放出します。しかし、この光は、波長(光の色)や位相(光の進むリズム)がばらばらで、まとまりがありません。
このばらばらな光が「誘導放出」によって同じ波長・位相・進行方向の光になります。誘導放出とは、放出された光が他の高エネルギー状態の電子に影響を与え、同じ性質を持つ光を新たに生み出す現象です。このプロセスが繰り返されることで、性質が揃った光が増幅されます。また、「反転分布」と呼ばれる「高エネルギーの電子が低エネルギーの電子よりも多く存在する状態」を作り出すことで、誘導放出が優勢になり、より光が増幅されます。
さらに、光共振器という装置を使用し、光を繰り返し反射させることで波長や位相を整え、強度を増幅させます。一方のミラーには半透過性を持たせ、そこから均整の取れた光を外部へ送り出すことで、レーザー光が生成されるのです。
レーザー光は、単色性(一定の波長)、指向性(特定方向への集中)、干渉性(波長と位相が揃っている)という特徴を持ちます。これにより、高エネルギー密度が実現し、工業の精密加工や医療の外科手術、通信分野の情報伝送など幅広い用途に活用されています。
レーザー加工の基本メカニズム
レーザー加工は、レーザー光の高いエネルギーを材料に集中的に照射して行われる加工方法です。この技術では、レーザー光のエネルギーが材料表面に吸収され、局所的に非常に高い温度を発生させます。この熱エネルギーを利用して、材料の状態を変化させたり、特定の反応を引き起こしたりすることで、さまざまな加工を行います。
加工の基本原理は、材料がレーザー光のエネルギーを吸収し、その結果として「溶融(材料が溶ける)」や「蒸発(材料が気化する)」といった現象が発生することです。例えば、レーザー切断では、材料を溶かしてその部分を除去することで切断が行われます。一方、レーザー穴あけでは、瞬間的な蒸発によって微細な穴を形成します。
さらに、特定の条件下では、レーザー光が化学反応や光化学反応を引き起こすことがあります。例えば、金属の切断に酸素を併用することで、金属と酸素が反応して発熱し、切断効率が向上する「酸素レーザー切断」が行われます。また、特定のプラスチックやポリマーでは、レーザー光が分子の化学結合を直接分解する「光化学反応」を利用して加工を進めます。
これらの現象がレーザー加工の精密性を支える要因です。レーザー光は、非常に狭い範囲にエネルギーを集中させることができるため、加工対象の材料に影響を与える範囲を極限まで小さく抑えることができます。
その結果、ミクロン単位の加工や、複雑な形状の形成が可能となり、工具が直接材料に触れないため、摩耗がなく清潔で、金属、プラスチック、セラミックスなど多様な材料に対応可能です。
レーザー加工機の主な構成要素
レーザー加工機は、大きく分けて三つの重要な構成要素から成り立っています。これらの要素が連携することで、高精度な加工を実現しています。
レーザー発振器
レーザー光を生成する装置であり、レーザー加工機の心臓部です。レーザー媒質の違いにより、CO2レーザーやファイバーレーザー、YAGレーザーなど、様々な種類が存在します。
CO2レーザーは炭酸ガスを媒質として使用し、非金属材料の加工に適している一方で、ファイバーレーザーは光ファイバー内で光を増幅させる方式で、金属加工において高い効率性を発揮します。YAGレーザーはイットリウム・アルミニウム・ガーネットの結晶を使用し、パルス発振による精密加工が得意です。
光学系システム
光学系システムは、レーザー加工においてレーザー光を正確に制御し、加工対象に照射するための重要な構成要素です。反射ミラーは、レーザー光を効率よく伝送する役割を担います。
これらのミラーにはレーザー光の波長やエネルギーに適したコーティングが施されており、光のロスを最小限に抑えます。一方、集光レンズはレーザー光を特定の焦点距離に集めることで、エネルギーを高密度に集中させます。
焦点距離やレンズの種類は加工の用途に応じて選ばれ、微細な加工や広範囲の均一な加工が可能です。これらの光学部品は高精度に配置される必要があり、少しのズレでも加工精度に影響を与えるため、アライメントの正確さが求められます。
さらに、レーザー光の高出力に耐える熱管理や保護コーティングの施された光学部品が使用されます。このように、光学系システムはレーザー加工の精密性と効率性を支える重要な技術です。
制御システム
制御システムはレーザー加工機の中枢であり、加工全体の動作を統括する重要な役割を担います。数値制御(NC)技術を活用し、XYZ軸方向の加工ヘッドの位置をミクロン単位で正確に制御することで、加工対象へのレーザー光の照射位置を高精度に設定し、精密な切断や穴あけを可能にします。
また、制御システムはレーザー出力や加工速度の調整も行います。材料の特性や加工内容に応じて、出力と速度をリアルタイムで最適化し、薄い材料の精密加工から厚い金属板の高速切断まで対応可能です。
さらに、加工条件を管理するデータベース機能も備えています。材質や板厚に応じた最適な設定をあらかじめ登録できるため、簡単に条件を再現でき、一貫した品質を維持できます。
最新のシステムではタッチパネル式の操作画面が採用され、直感的な操作が可能です。また、加工中の異常を検知して即座に停止する安全機能や、加工品質をリアルタイムで監視する機能も備えており、安定した生産と高品質な加工を支えています。
レーザ加工機でできること
レーザー加工機による切断は、金属から樹脂まで多様な材料に対応可能です。レーザー光の高いエネルギーにより、材料を溶融または蒸発させて切断を行います。切断面が美しく、複雑な形状も正確に加工できることが特長です。
切断加工
レーザー加工機による切断は、金属から樹脂まで多様な材料に対応可能です。レーザー光の高いエネルギーにより、材料を溶融または蒸発させて切断を行います。
切断面が美しく、複雑な形状も正確に加工できることが特長です。また、接触を伴わない加工のため、材料への負荷が少なく、繊細な部品の加工にも適しています。
マーキング・刻印加工
マーキングは材料表面にレーザーを照射し、文字や図形を描く加工方法です。レーザーの出力を調整することで、材料表面を変色させたり、微細な凹みを作ったりすることができ、製品の識別番号やロゴマーク、装飾的なデザインなど、様々な用途に活用されています。耐久性が高く、経年変化が少ないことも大きな特徴です。
溶接加工
レーザー溶接は、高密度なエネルギーを局所的に照射することで、金属材料を接合する加工方法です。従来の溶接方法と比べて、熱影響が小さく、変形が少ないという利点があります。また、深い溶け込みが得られるため、一度の照射で厚い材料も溶接することができます。精密な制御により、微細な部品から大型の構造物まで幅広い溶接加工に対応できるのも大きな特徴です。
表面処理加工
レーザーによる表面処理は、材料の表面特性を改善する加工方法です。表面の硬化処理や、微細な凹凸を形成することで摩擦特性を変更するなど、様々な目的で活用されています。また、表面のクリーニングや酸化膜の除去にも使用され、他の加工方法では難しい精密な表面処理を実現できます。
レーザ加工機の強み
従来の機械加工と比較して、レーザー加工機は非接触での加工が可能です。これにより、工具による材料への機械的な負荷がなく、高精度な加工を実現できます。
また、熱影響が最小限に抑えられるため、材料の変形や歪みが少なく、美しい仕上がりが特徴です。このような利点があり、レーザー加工は様々な産業で採用されています。
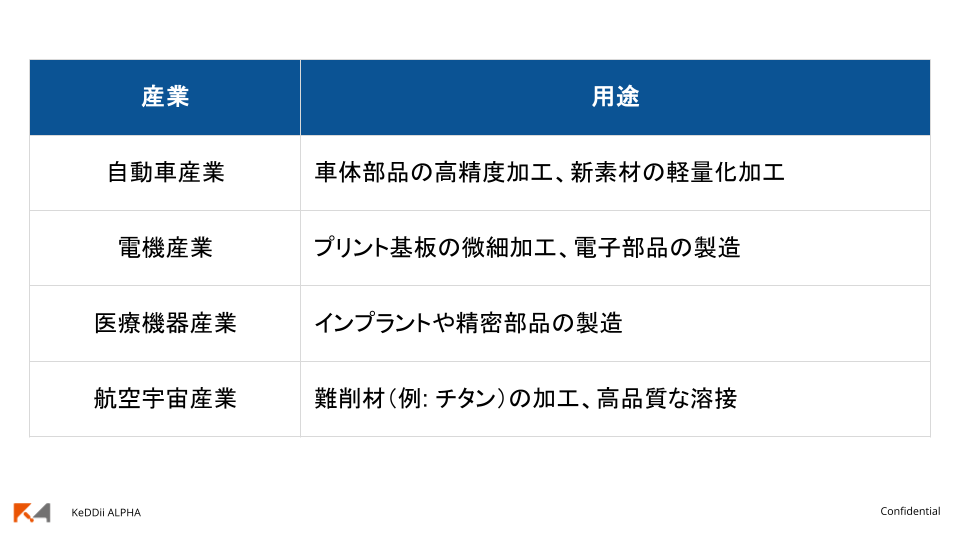
従来の加工方法との比較
レーザー加工機と従来の機械加工方法を比較すると、精度、品質、生産性、コストなど、多くの面で優位性が見られます。特に非接触加工という特徴は、従来の加工方法では実現できない利点をもたらしています。
精度と品質面での優位性
従来の機械加工と比較して、レーザー加工機は非接触での加工が可能です。これにより、工具による材料への機械的な負荷がなく、高精度な加工を実現できます。
また、熱影響が最小限に抑えられるため、材料の変形や歪みが少なく、美しい仕上がりが特徴です。特に微細加工においては、レーザービームを数十マイクロメートル単位まで絞り込むことができ、従来の機械加工では難しかった精密な加工が可能です。複雑な形状でも、プログラミング制御により正確な加工を実現できます。
生産性とコスト面での優位性
レーザー加工機は、高速加工が可能で、複雑な形状でも一度のプログラミングで連続的に加工でき、工具交換が不要なため、段取り替え時間を大幅に削減できます。また、自動化システムとの親和性が高く、24時間連続運転による生産性の向上も実現可能です。
溶接機は数百万で、切断加工機は数千万~1億の初期費用がかかります。一方、工具費用や消耗品費用が少なく、長期的な運用ではコスト効率に優れています。加えて、高い加工精度により不良品の発生を抑制でき、材料のムダを最小限に抑えることが可能です。
環境負荷低減効果
製造業における環境負荷の低減は、現代の重要な課題の一つです。レーザー加工機は、この課題に対して効果的なソリューションを提供しています。
レーザー加工機は、切削油や冷却液が不要なため、環境負荷を大幅に低減でき、高効率な加工により消費電力を抑えるため省エネルギー性能に優れています。加工時の材料ロスが少なく、廃棄物の削減も可能です。
さらに、非接触加工のため粉塵の発生が少なく、作業環境の改善にも効果があります。これらの特徴により、環境に配慮した製造プロセスの構築が可能です。
レーザ加工機の種類
レーザー加工機には、発振方式や波長の違いにより、様々な種類が存在します。それぞれに特徴があり、加工対象や目的に応じて最適な選択が必要です。
ここでは、主要な3種類のレーザー加工機について、その特徴と用途を詳しく解説します。
CO2レーザー加工機の特徴
CO2レーザー加工機は、最も広く普及しているレーザー加工機の一つです。非金属材料の加工に優れた性能を発揮し、特にアクリルや木材の加工で高い評価を得ています。
波長10.6μmの遠赤外光を使用するCO2レーザーは、非金属材料の加工において優れた性能を発揮します。特にアクリル、木材、布などの非金属材料だけでなく、ガラスやゴムなどにも対応可能で、比較的安価な導入コストも特徴です。
メンテナンス性が良く、出力範囲も広いため、様々な加工現場のニーズに対応することができます。
ファイバーレーザー加工機の特徴
ファイバーレーザー加工機は、近年急速に普及が進んでいる次世代型のレーザー加工機です。高効率で安定した出力特性を持ち、金属加工において優れた性能を発揮します。
波長1.06μm前後の近赤外光を使用するファイバーレーザーは、アルミニウムや真鍮、銅などの高反射材の金属材料加工において卓越した性能を示します。高いビーム品質と集光性を持ち、省エネルギーで運転コストが低いことも大きな特徴です。さらに、メンテナンスフリーで長寿命であり、小型・軽量な設計により設置スペースの節約も可能です。
YAGレーザー加工機の特徴
YAGレーザー加工機は、イットリウム・アルミニウム・ガーネット(YAG)を媒質とした固体レーザー技術を利用しており、特に金属や樹脂の加工において高い性能を発揮します。
波長1.06μmの近赤外光を使用するYAGレーザーは、金属材料の精密加工に適しており、パルス発振による微細加工が得意で、高いピークパワーを実現でき、光ファイバーでの伝送が可能です。
金属部品のスポット溶接やシーム溶接など特殊加工においても、優れた性能を発揮するでしょう。
用途別の最適な選び方
レーザー加工機の選定は、以下のように加工対象材料、要求される精度、コスト、生産規模など、様々な要因を考慮して行う必要があります。ぜひ用途に合わせて最適なものをお選びください。
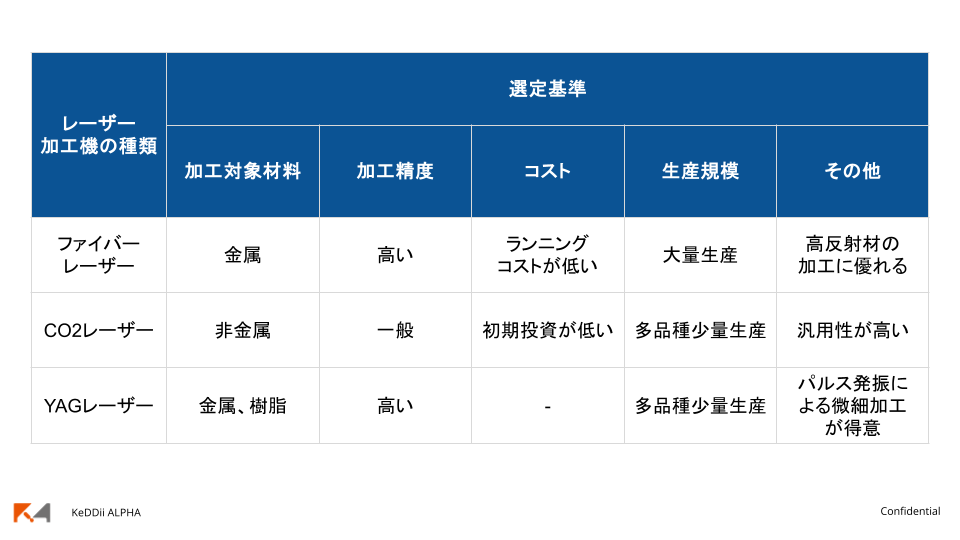
もしファイバーレーザー加工機を用いた金属加工にご興味のある方は、ぜひKeDDiiALPHAもご検討ください。
⇒ ネットでレーザーカット板金オンラインツールといえばKeDDiiALPHA
レーザ加工機を導入・使用するときの注意点
レーザー加工機は高度な加工を実現する一方で、適切な管理と運用が必要な装置です。
導入時の検討事項から日常的な使用上の注意まで、安全で効率的な運用のために重要なポイントについて解説します。
導入時の検討事項
レーザー加工機の導入には、様々な要素を総合的に検討する必要があります。適切な機種選定は、その後の生産性や運用コストに大きく影響するので注意が必要です。
まず設置場所の確保が重要です。本体の設置スペースだけでなく、材料の搬入出や作業スペース、メンテナンス時の余裕も考慮に入れる必要があります。また、電源設備や排気設備などのインフラ整備も必須です。
導入コストについては、本体価格に加えて、付帯設備や工事費用、教育訓練費用なども含めた総合的な予算計画が必要です。さらに、ランニングコストとして電力費、消耗品費、メンテナンス費用なども考慮に入れなければなりません。
特に、切断加工機の導入には数千万~1億程度の予算が必要です。その点をよく考慮して導入するか、外注するかを判断するといいでしょう。
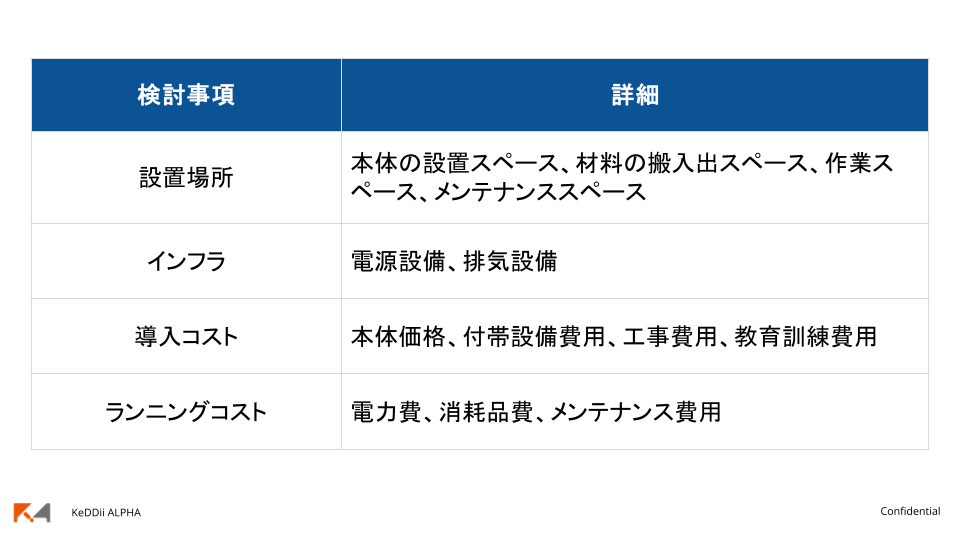
安全管理の重要性
レーザー加工機の使用にあたっては、作業者の安全を確保するための適切な管理体制が不可欠です。レーザー光は極めて高エネルギーであるため、直接の照射や反射光への曝露は重大な事故を招く可能性があります。このため、作業者は事前に十分な安全教育を受けることが求められます。
特に重要なのは、防護具の使用です。保護メガネは、レーザー光が目に直接入ることを防ぐために欠かせません。さらに、作業区域の立ち入り制限を徹底し、作業中に関係者以外が誤って危険な区域に入ることを防止する仕組みを整備することが重要です。
加えて、加工時に発生するヒュームや粉塵への対策も欠かせません。特定の材料を加工する際には、材料が蒸発したり燃焼したりすることで微粒子や有害ガスが発生することがあります。これらの対策としては、適切な排気システムを設置することが効果的です。排気システムを定期的にメンテナンスすることで、その機能を維持し、作業環境の安全性を確保する必要があります。
また、レーザー加工機を使用する現場では、定期的な点検を行うことでトラブルの発生を未然に防ぐことが重要です。特に、光学系のレンズやミラーに汚れが付着すると加工精度が低下し、思わぬ不良や故障を引き起こす可能性があります。そのため、これらの部品を清掃し、常に良好な状態を保つ努力が求められます。
このような管理と運用を徹底することで、レーザー加工機の性能を最大限に引き出しながら、安全かつ効率的な作業環境を維持することが可能になります。安全性の確保は、生産性向上にもつながる重要な要素であるため、継続的な見直しと改善を行うことが大切です。
日常的なメンテナンス
レーザー加工機の性能を維持し、長期的な運用を実現するためには、適切なメンテナンス管理が欠かせません。日常点検から定期的な保守まで、計画的な管理が重要です。
光学系の清掃は特に重要で、レンズやミラーの汚れは加工品質に直接影響します。定期的な点検と清掃により、常に最適な状態を維持する必要性を忘れてはいけません。また、各部の摩耗や劣化状況を確認し、必要に応じて部品交換を行うことで、突発的な故障を防ぐことができます。
加工データの管理も重要な要素です。最適な加工条件のデータベース化や、定期的なバックアップにより、安定した加工品質の維持と効率的な運用が可能となります。
トラブル対応と予防措置
レーザー加工機の運用において、トラブルの発生は避けられません。しかし、適切な予防措置と迅速な対応により、影響を最小限に抑えることができます。
トラブル発生時の対応手順をマニュアル化し、作業者全員で共有することが重要です。また、予備部品の確保や、メーカーサポート体制の確認など、事前の準備も徹底します。
加えて、定期的な点検データの記録と分析により、潜在的な問題を早期に発見できます。予防保全の観点から、部品の寿命や劣化傾向を把握し、計画的な保守を行うことで、突発的なトラブルを防げるでしょう。
まとめ
レーザー加工機は、非接触加工による高精度化や高速化、さらに自動化による生産性向上を実現します。製造現場では、レーザー加工によって品質向上やコスト削減が可能です。
しかし、レーザー加工機の導入には、機種選定や設置環境、安全管理、メンテナンスなど、多くの要素を慎重に検討する必要があります。溶接機は比較的安価で導入ハードルは低い一方、切断加工機は導入に数千万~1億程度の予算が必要であり、ハードルが高いです。そのため、外注が現実的な選択となる場合が多いでしょう。
KeDDii ALPHAのような外注サービスを活用すれば、切断加工も安価かつスムーズに依頼でき、短納期での対応が期待できます。もし自社でのレーザー切断加工機の導入が難しい場合は、ぜひKeDDii ALPHAへお問い合わせください。自動見積もりが可能なので、お手軽にご利用いただけます。「短期で加工/納品して欲しい」というご要望にもお応えいたしますので、ぜひご相談ください。
▼会員登録して自動見積もりする